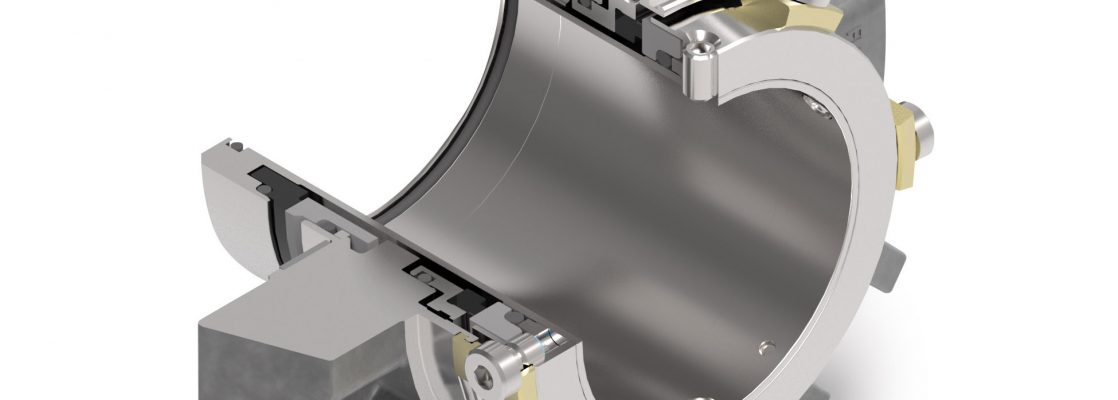
Mechanical seals are critical components in many industrial applications, including pumps, compressors, and mixers. They play a vital role in preventing fluid leakage and maintaining system integrity. One of the key factors that determine the performance of mechanical seals is the working length, which refers to the axial distance between the sealing faces.
In this article, we will explore the working length of mechanical seals in detail, including its definition, importance, and factors that affect it. We will also discuss how to determine the optimal working length for specific applications and provide some practical tips for maintaining mechanical seals.
What is the Working Length of Mechanical Seals?
The working length of a mechanical seal is the axial distance between the sealing faces when the seal is in operation. It is typically measured from the back of the stationary seal face to the front of the rotating seal face. The working length is a critical parameter that affects the sealing performance of the mechanical seal.
Importance of Working Length in Mechanical Seals
The working length of a mechanical seal is crucial for several reasons. First, it determines the amount of contact between the sealing faces, which affects the sealing efficiency and the amount of friction generated. Second, it affects the heat dissipation and cooling of the seal faces, which can impact the seal’s lifespan and reliability. Finally, the working length can also affect the axial movement of the shaft and the stability of the rotor.
Factors Affecting Working Length
Several factors can affect the working length of mechanical seals, including the seal design, operating conditions, and installation parameters. For example, the type of seal face material, the seal face geometry, and the spring force can all impact the working length. Similarly, the temperature, pressure, and speed of the fluid being sealed can affect the working length by causing thermal expansion or contraction of the seal faces.
Determining Optimal Working Length
To determine the optimal working length for a specific application, several factors must be considered. These include the seal design, the operating conditions, and the fluid being sealed. In general, the working length should be set to achieve the desired sealing efficiency while minimizing friction and wear. It should also be optimized to ensure adequate cooling and heat dissipation.
Tips for Maintaining Mechanical Seals
Proper maintenance is essential for ensuring the optimal performance and lifespan of mechanical seals. Some practical tips for maintaining mechanical seals include:
- Regularly inspecting the seal faces for wear, damage, or contamination.
- Ensuring that the seal faces are properly lubricated and cooled.
- Checking the seal springs and other components for signs of wear or damage.
- Monitoring the operating conditions and adjusting the working length as needed.
Conclusion
The working length of mechanical seals is a critical parameter that affects the sealing efficiency, friction, and lifespan of the seal. By understanding the factors that affect the working length and how to optimize it for specific applications, engineers can ensure optimal performance and reliability. Proper maintenance is also essential for ensuring the long-term performance of mechanical seals.